Istnieje wiele głośnych przykładów wycofywania produktów, będących skutkiem błędu w projektowaniu lub produkcji. Błędy dyskutowane są na forum publicznym, a producenci czy dostawcy stawiani są w złym świetle, najczęściej jako niezdolni do zapewniania bezpieczeństwa produktu. Metoda FMEA – Failure Mode and Effect Analysis – to analiza przyczyn i skutków powstałych wad czy też błędów. Ma również na celu umożliwienie przedsiębiorstwom przewidywania awarii już na etapie projektowania. Opracowana w latach 50-tych, FMEA była jedną z najwcześniejszych metod poprawy niezawodności. Pionierem stosowania tej metody było NASA, przygotowujące się do misji kosmicznych „Apollo”. FMEA pomagała w weryfikowaniu projektów elementów statków kosmicznych, aby zapewnić jak najwyższą jakość oraz bezpieczeństwo pasażerów. Dzisiaj nadal jest bardzo skuteczną metodą minimalizowania możliwości niepowodzenia, najczęściej stosowaną w przemyśle motoryzacyjnym.
Na czym polega FMEA?
Analiza rodzajów i skutków błędów to uporządkowane podejście do wykrywania potencjalnych awarii, które mogą występować w projektowaniu produktu lub procesu. Metoda ma na celu identyfikację, ustalanie priorytetów i ograniczenie trybów awaryjnych. FMEA nie jest jednak substytutem dobrej inżynierii. Zamiast tego poprawia ją, wykorzystując wiedzę i doświadczenie zespołu. Chodzi tak naprawdę o ciągłe doskonalenie procesów oraz produktów dzięki systematycznemu analizowaniu i wdrażaniu poprawek. Takie systematyczne działania eliminują wady już u źródła, tym samym poprawiając właściwości wyrobu. Istnieją dwie szerokie kategorie FMEA – produktowa oraz procesowa.
FMEA procesu i produktu – co je łączy, a co dzieli?
FMEA procesu (PFMEA) odkrywa awarię, która ma wpływ na jakość produktu, zmniejszenie niezawodności procesu oraz mogłaby zagrażać bezpieczeństwu środowiska lub klienta. Pod uwagę bierze się czynniki takie jak:
- metody stosowane podczas procesu,
- czynniki ludzkie,
- użyte materiały,
- maszyny używane podczas procesu,
- czynniki środowiska wpływające na wydajność procesu.
FMEA projektu natomiast bada możliwości nieprawidłowego działania produktu, skrócenia czasu jego użytkowania, a także kwestie bezpieczeństwa oraz regulacji prawnych. Pod uwagę bierze się czynniki takie jak: geometria, właściwości materiału, tolerancja czy profil użytkownika. Szczegółowa metodologia zależy jednak od konkretnych procedur stosowanych przez daną organizację. Natomiast obie wyżej wymienione analizy pozwalają na znaczące obniżenie kosztów wyrobów, których jakość jest wątpliwa lub zła.
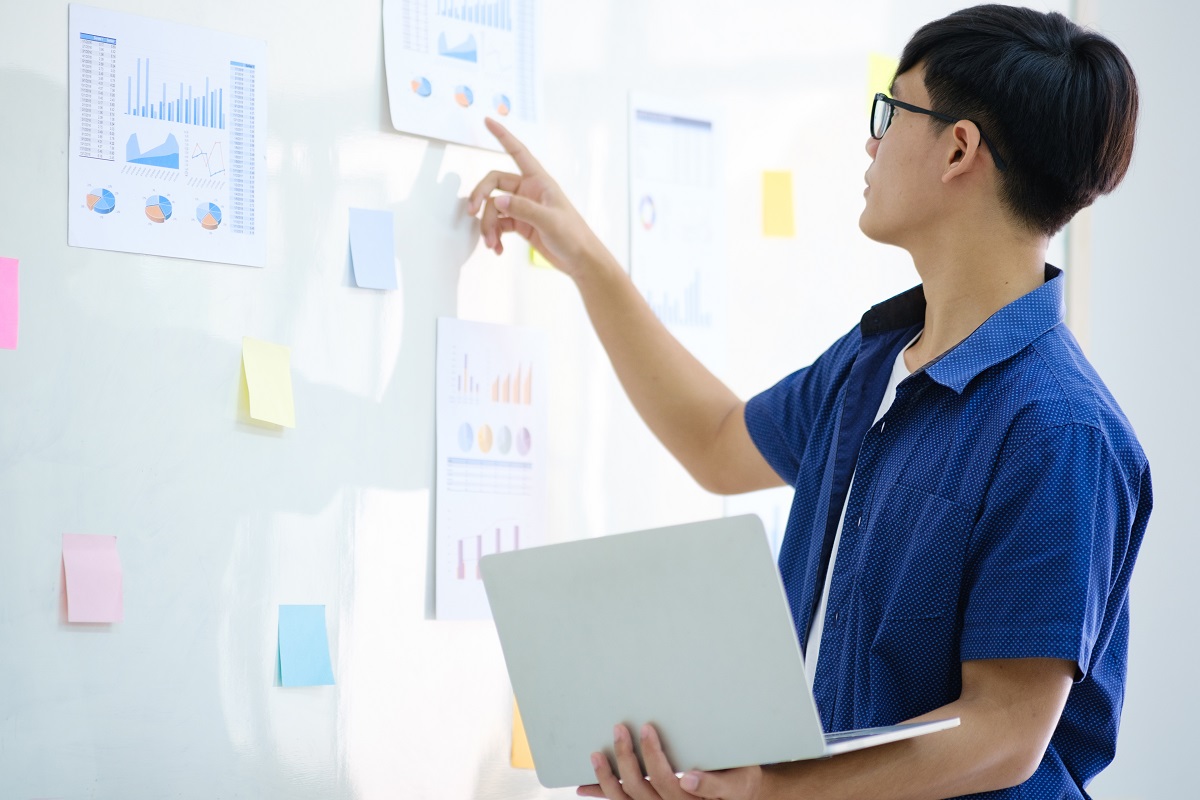
Jak wyglądają etapy oceny?
Analiza FMEA jest niezwykle uniwersalna. Może być stosowana nie tylko do optymalizacji produktów, ale również procesów, a także zarządzania ryzykiem. Dla wszystkich zastosowań wspólny jest jednak sposób przeprowadzania analizy. Na początku definiowane są cele badania oraz jego zakres, a następnie tworzony jest zespół ekspertów mających podjąć się oceny. Dokonują oni analizy jakościowej i ilościowej. Następnie tworzą zestaw działań mających przynieść poprawę w określonej dziedzinie, a także chroniących przed ponownym pojawieniem się błędu. Pozostaje jedynie ich wdrożenie, a następnie nadzorowanie.
Jak ułatwić sobie analizę obiektu?
Badanie jest łatwiejsze, jeśli badacz dobrze zna analizowany obiekt. W tym celu może on podzielić go na mniejsze części. Jeśli obiektem badania jest na przykład produkt, można przeanalizować jego skład, właściwości oraz zastosowanie. Każda część podlega następnie analizie z punktu widzenia liczby i rodzaju wad, możliwych problemów oraz ograniczeń wynikających z użytkowania. Analiza jakościowa bada przyczynę występowania wad oraz ich skutek. Z kolei badanie pod kątem ilościowym uwzględnia trzy główne czynniki, w tym prawdopodobieństwo wystąpienia, trudność wykrycia oraz znaczenie skutku wady. Zebrane dane podstawia się do odpowiednich wzorów. Wynik jest następnie porównywany z ustalonymi kryteriami oceny.
W jaki sposób dokonywana jest poprawa?
Udoskonalenie produktu jest możliwe poprzez trzy główne kierunki, a więc zmniejszenie prawdopodobieństwa wystąpienia wady lub znaczenia skutku albo poprawę skuteczności wykrywania wady. Podczas jednego badania można przeanalizować więcej niż jedną wadę. Dzięki temu działania naprawcze są opracowywane przy uwzględnieniu szerszego punktu widzenia.
Czego mogą dotyczyć wady produktu?
Nieprawidłowości mogą występować w zakresie funkcji, jakie dany produkt ma wykonywać, a także sposobu jego użytkowania. Za wadę produktu uznaje się także trudności związane z obsługą. Analizie można poddać poziom łatwości wykonania naprawy w przypadku wystąpienia awarii. Istotna jest także technologia zastosowana w konstrukcji danego wyrobu. Analiza FMEA jest wykonywana w szczególności w przypadku wprowadzania na rynek nowych wyrobów oraz w przypadku produktów wykorzystywanych w trudnych warunkach. Stosuje się ją także w pierwszej fazie projektowania procesów technologicznych, jeszcze przed rozpoczęciem produkcji seryjnej.